RotoGro have recently joined The FarmTech Society as members. We’re delighted to have this unique system and company as part of our network. We sat down with CEO Michael Di Tommaso to talk about their activities and plans for the future
FTS: Hi Michael, thanks for joining and for taking the time to talk with us. To start with, can you tell us a bit more about your systems, particularly what makes them so unique?
RotoGro:
Thanks for having me.
RotoGro is a technology partner in the indoor vertical farming marketspace, offering its full-facility state-of-the-art cultivation solutions to this industry.
Our unique market position is due to the competitive advantage of its technology. The RotoGro Rotational Garden Systems represent a sort of technological revolution in the space. In essence, they are a commercial-scale, cutting-edge crop cultivation solution set to lead the charge in sustainable, urban indoor vertical farming.
The intrinsic design of the Garden Systems permits RotoGro to offer indoor vertical farmers a technology that not only significantly increases yield per m2, but also significantly reduces the operational expenditure when compared to other indoor vertical farming technologies, including advanced flat deck, stacked growing methods.
The Garden Systems maximize plant surface grow area by situating a spherical garden around a centrally placed, proprietary lighting system. The Garden Systems can be stacked one on top of another, while also being stacked side-by-side, maximizing yield per m2 when compared to the floorspace footprint of which they occupy. The result is maximized utilizable plant surface grow area within the cultivation space.
FTS: Capex is obviously a major challenge for our industry, but as a result, opex sometimes gets overlooked, or at least not given adequate attention. You offer what you describe as substantially reduced operating costs. Can you tell explain that a little?
RotoGro:
Absolutely.
The Garden Systems encompass patented and patent pending designs that allow indoor vertical farmers utilizing this technology to decrease their operational expenditure. As we all know, Indoor vertical farming traditionally demands significant electricity usage, and with this comes significant cost. This is the highest operational cost associated with indoor vertical farming operations, along with labour.
RotoGro’s technology decreases the traditionally required electricity usage in two ways: first, the intrinsic design of the Garden Systems – situating a spherical garden around a centrally placed proprietary lighting system – as mentioned, optimizes the use of light to growing surface area; second, the centrally placed lighting system incorporates a patented, ducted cooling system, which draws external air through the glass light tube in which the light sits, and then disperses this heated air to another location within the facility or to the exterior of the facility (depending on the location of the facility). By removing the heat generated by the lights through the ducted system, the air conditioning associated with cooling the heat generated from the lights decreases, and therefore decreases the air conditioning costs (and therefore the humidification and dehumidication costs) associated with controlling the environment within the cultivation area. Further to this is that the ducted heat generated by the lights may be used to heat other parts of the facility, lowering heating costs, depending on the location of the facility, for example in Canada during the winter.
RotoGro’s proprietary software systems are designed to allow the Garden Systems to be a plug and play operation by controlling of all the mechanics within the Garden Systems, the environmental parameters within the cultivation areas, and the plant nutrient management systems, all on screen and in real-time. These parameters can be pre-set, automating the entire cultivation process facility wide. This, in turn, significantly reduces the labour traditionally required for indoor vertical farming, which positively contributes to workflow efficiencies and labour costs. Moreover, RotoGro’s Plant Nutrient Management System (or, Fertigation System, as we like to call it) delivers to the Garden Systems the water or water/nutrient solution necessary to feed the plants. The entire process is again controlled by RotoGro’s software system and its advanced design, recycling up to ninety-eight percent (98%) of the water used to feed the plants, further decreasing the operational expenditure and other negative environmental impacts when compared to other farming techniques.
Further, the Garden Systems utilize RotoGro’s proprietary LED lighting system. RotoGro’s plant science team has optimized the LED spectrum for enhanced plant growth. RotoGro’s software provides cultivators with the ability to adjust the LED Lighting System’s spectrum and intensity, as well as automate the lighting process within the Garden systems throughout the cultivation process as well.
We’ve also designed and implemented at our research and design facility an automated guided vehicle system. This system autonomously delivers growing trays from the propagation area to the multi-stacked Garden Systems, loading the trays into the units. And Conversely, once the crop is ready to harvest, the same AGVs remove the growing trays from the Garden Systems and shuttles them off to the harvesting area. This system is also controlled by RotoGro’s software, which allows operators to pre-program the loading and unloading schedules, removing the need for unnecessary human intervention from the cultivation area, reducing the potential for the introduction of pests and pathogens into this area, while simultaneously decreasing the labour opex. It’s truly a win-win.
FTS: RotoGro have been providing solutions to the ag industry since 2003, making you veterans of this still relatively young industry! How have things changed in the time?
RotoGro:
Things have changed considerably. Most important to this conversation was the Company’s shift to steadily focus on producing technology for the indoor vertical farming perishable food (or produce) sector. We analyzed the space to understand how our technology could change the landscape and developed a technology to cater to this. We understood quite quickly that the premise of our technology offered significant yield per m2 advantages than when compared to other technologies in the space. Putting that aside, we went one step further and redesigned the size of our already existing Garden Systems to optimize the operational expenditures: mainly, power consumption. By offering operators a solution to this problem by maximizing the light to grow surface area ratio, and then linking this with our patented hot air removal lighting system to reduce HVAC loads, we began to really appreciate our competitive advantage in the space. Moving past the “cool factor”, RotoGro’s technology truly became what we believe to be the viable solution to sustainable indoor vertical farming given its ability to increase yield per m2, while significantly decreasing the opex when compared to the other array of technologies penetrating the space.
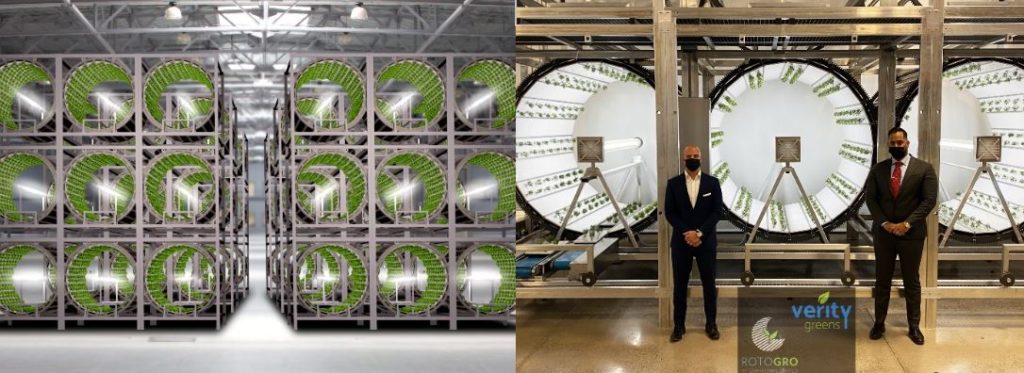
FTS: What does the future hold for RotoGro? What’s next and what are your plans in the medium and long term?
Member:
This is a great question. As a team, we work together to understand not only where the industry is headed, but to foresee why the industry is headed in that direction. This allows us to predict and put in place solutions to cater to the why. Because of this, we are currently looking to other “green” and progressive industries to predict the next shift.
In turn, what’s next for the company is to construct a commercial-scale indoor vertical farm with our partners in the space. The medium-term goal is to penetrate the space globally, building relationships with local players in various jurisdictions that require our technology to move forward with indoor vertical farms that provide for long-term sustainability. This will also involve industry relevant synergistic opportunities in renewable energy, and the like, something I think this industry isn’t quite utilizing efficiently. Our long-term objectives are to be instrumental leaders in the space whereby RotoGro’s technology would be a major facet in establishing a global “green” supply chain in the agricultural industry. In essence, RotoGro as a whole, is prepared to provide solutions to the problems we face today, but we’re also geared up to put in place solutions to the problems that we will face tomorrow. Our advantaged engineering expertise, coupled with our plant science capabilities, puts is into a versatile position and really fosters our competitive advantage in the space, something we recognize and will certainly use to provide the most efficient and effective agtech solutions to achieve our goals.
FTS: Michael, thanks so much for taking the time to have a chat with us. We’re delighted to have you with us and will be watching RotoGro’s progress with great interest!
Member: It’s my pleasure. Thank you.
For RotoGro
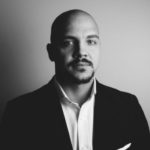
Michael Di Tommaso - Chief Executive Officer
We want you, our readers, to know more about who our members are and what they’re doing. So we put together the FTS finds out more series, to do just that!
——–